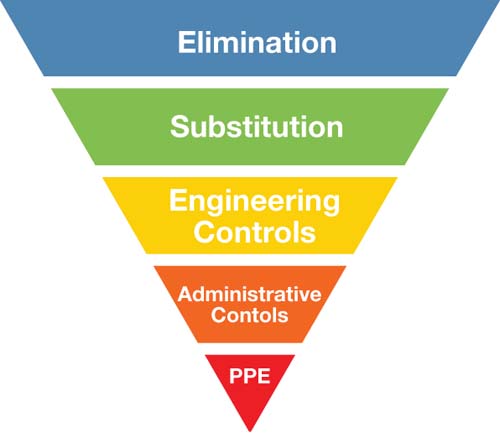
Responding is Matt Block, director of health and safety services, Magid Glove & Safety Mfg. Co. LLC, Romeoville, IL.
Obviously, the standard is familiar to all safety managers: OSHA’s Hierarchy of Controls. It tells us that personal protective equipment is the least effective mitigation solution and the last thing we should employ to safeguard workers’ hearing.
Accordingly, we start with elimination. Is it possible to eliminate the hazard entirely? Is the equipment obsolete? Is there a better way to accomplish the task that doesn’t involve the current level of noise?
Next, we move to substitution. Is there a newer version of the equipment that produces a lower level of noise? This may be a more expensive alternative if you’re replacing entire pieces of equipment, but in some cases, it can be the most effective. Sometimes, it’s a simple matter of equipment maintenance. Review your logs to see if replacing one or more parts might fix the issue.
Once you know what equipment you have to work with, you can move on to engineering controls. This can take several different forms. If it’s possible to identify a particular part of a machine that’s causing a great deal of vibration or noise, you can look into adding measures to dampen that portion. Sound absorption techniques such as sound baffles or insulators to absorb some of the noise in the area can be effective. It may even be possible to add shock absorbers or sound dampening materials to portions of the equipment to dampen the noise before it reaches the room.
You can also work to contain the noise. You might move loud equipment to a separate room, or even con-struct a room around the equipment itself if it’s very large or in the middle of your facility.
This can be a double-edged sword, however, because the rest of your facility is protected from the noise, but workers who have to use the equipment may be in closer proximity and in an enclosed space, thereby increasing their noise exposure.
If you’ve done all you can with the hazard itself, it’s time to turn to administrative and work practice controls. The most common administrative control is to change workers’ schedules so they have less time exposed to the noise level. You should factor noise levels into your worker rotations just as you do ergonomic issues.
Work practice controls include setting up your facility so people aren’t working in noisy areas. This might mean putting your loudest equipment in an isolated place. If that’s not possible, you will look at the next step in your process to see how you might be able to move that.
For example, if you have a loud machine doing cutting, followed by an assembly step, rethink where that assembly can be done. Can you move the cut materials and assemble them in a quieter area?
Once you’ve controlled as much noise as possible, it’s time to consider PPE. Quality products are important, but equally important is training and reminders. Be sure everyone knows how to wear their hearing protection properly and that they understand the consequences of cutting corners.
Above all, remember that every application and environment is unique. Tackling your noise problems in this order, while sometimes thinking outside the box, is the path to preserving your workers’ hearing and good health.
McCraren Compliance offers many opportunities in safety training to help circumvent accidents. Please take a moment to visit our calendar of classes to see what we can do to help your safety measures from training to consulting.