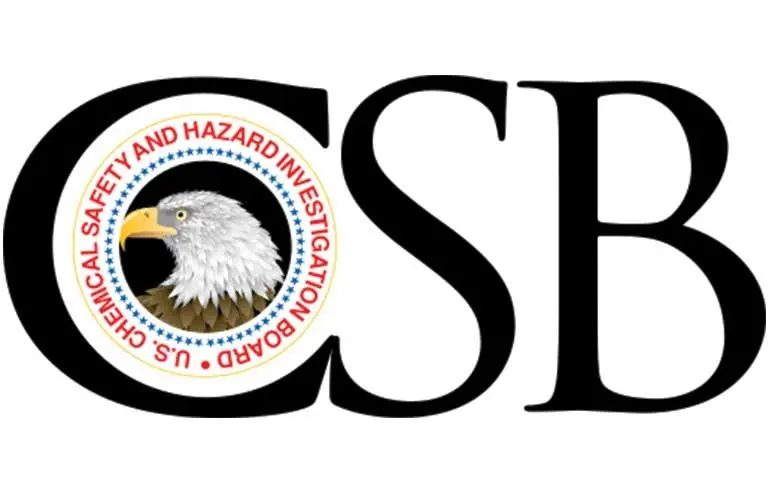
Washington — Establishing and implementing engineering controls as “preventive safeguards” during a process hazard analysis can help prevent liquid overflow and a possible chemical disaster, the Chemical Safety Board says.
The agency makes that conclusion in a recent final report on a fatal chemical release and fire in September 2022 at the BP-Husky Energy Refinery in Oregon, OH.
CSB investigators found that a fatal release of the flammable liquid naphtha resulted after two workers opened a pressurized vessel for emergency draining purposes. The vessel usually contained only vapor; however, “a series of cascading – and worsening – events throughout the day” contributed to the disaster, a CSB press release states.
This included more than 3,700 alarms sounding in the 12 hours before the incident, delaying responses and upsetting facility processes. The report suggests that the workers may have believed the vessel contained an amine-water solution – not naphtha.
CSB asserts that preventive safeguards such as a high-level interlock to close the naphtha feed valve to the absorber stripper tower “would have automatically stopped the identified liquid overflow events.” Instead, the facility relied on alarms “that require human intervention, emergency pressure-relief valves and downstream safety instrumented systems.”
Other lessons for the industry:
- Ensure – through training, clearly written procedures and other means – employees are clearly empowered to exercise stop-work authority and understand they’re expected to do so.
- Process hazard analyses should evaluate overfill hazards and consider scenarios in which a vessel may not overfill to the top but may instead overflow or backflow through other piping connections.
- Realize that abnormal situations introduce stress and may trigger poor decisions from operators. Think through situations before they occur and have plans in place. Define operating limits beyond which abnormal situation management procedures should be followed and clearly define those corrective actions to be followed to stop a chain of abnormal events.
- Ensure alarms are well justified.
- Create systems to ensure learnings from internal and external incidents are incorporated throughout the organization to prevent recurring failures.
“Nearly everything that could go wrong did go wrong during this incident,” CSB Chair Steve Owens said in the release. “The tragic loss of life resulting from this fire underscores the importance of putting in place the tools that employees need to perform tasks safely, such as stop-work authority, and having adequate policies, procedures and safeguards in place to effectively manage highly stressful abnormal situations, including alarm floods.”
McCraren Compliance offers many opportunities in safety training to help circumvent accidents. Please take a moment to visit our calendar of classes to see what we can do to help your safety measures from training to consulting.
Original article published by Safety+Health an NSC publication